Some time ago a musician from Curaçao contacted me because of an old Cello, he is actually not playing the instrument but does not want it to erode either. He asked me what can be done to keep it in as good as a condition as possible.
After receiving some pictures to get an idea about the conditions it was quite sure there were no big problems. It turned out that it was actually needed for a concert and because I’m based on Aruba I wasn’t able to help out with little fixes like changing the strings and fixing a missing piece at the endpin. Irrespective, the musicians found solutions to the problems.
I thought then that maybe the book was closed, but luckily not as I got the opportunity to work with an old and very well preserved patient at my working table. It was buried for a long period of time in storage and dust particles and didn’t get much attention until one day someone freed it out of that state and finally got to see a violin maker.
The first step for me was to check for any cracks or broken pieces. I noticed that there was a crack on the top, on the side of the soundpost but still far enough from the soundpost. The top of a Violin, Viola or Cello is most of the time made out of spruce. The wood is cut and used in a way that the veins follow all the way from top to bottom. Like that you get a good sound quality out of the instrument, what we would then call Tonewood. The way in which it is worked out is just a couple of millimeters thick that makes it at the same time delicate as well as good sounding. The soundpost is a kind of wooden stick, we adjust it to the sound body between back and top. It is placed lightly behind the bridge but because it is inside the instrument, you won’t see it as long as you don’t search for it.
This piece of wood is transmitting the vibration between the back and the top. Because wood is always working and moving, if the tension of the soundpost is for example too strong and the spruce is a little delicate in its structure, it can cause a soundpost-crack. Those cracks can get very uncomfortable if not treated. A big repair / restoration with adding a sound post patch would then be the next step. In this case luckily there weren’t any risk, the crack was already protected and patched.
After, I checked if the top or back were in some parts loose from the rips. That is something that can happen very easy with the passing of the years and change in climate. For these cases I would use natural bone/skin glue that is not too strong. For cases where the wood needs to move or deform, this glue can crack open more easy instead of letting the wood crack by itself.
In general, bodies of a Violin, Viola or Cello are made out of different types of wood (for example maple for back and rips and spruce as I mentioned before for the top). Those woods age differently and can create areas of stress due to differences in density that consequently affect the rate of expansion or contraction. That’s why it is common for an instrument to have openings from the top to the rips or the back and the rips.
This Cello is very well kept and didn’t have any of that. Everything was looking good and there weren’t any additional cracks, just the varnish that did not get much attention over the years. All original, barely small zones of touch ups but lots of old dirt. It also got some bumps so the varnish definitely needed to be taken care of.
I gave the instrument a nice clean and touch up job to let it shine again and properly represent the beauty of its sound. I want to thank the customer from Curaçao for doing business and sincerely hope to see this wonderful instrument back in my workshop in the future.
With this encounter I am also announcing the opening of our new professional photography corner, especially designed to take professional pictures of instruments. With or without a musician, doesn’t matter.
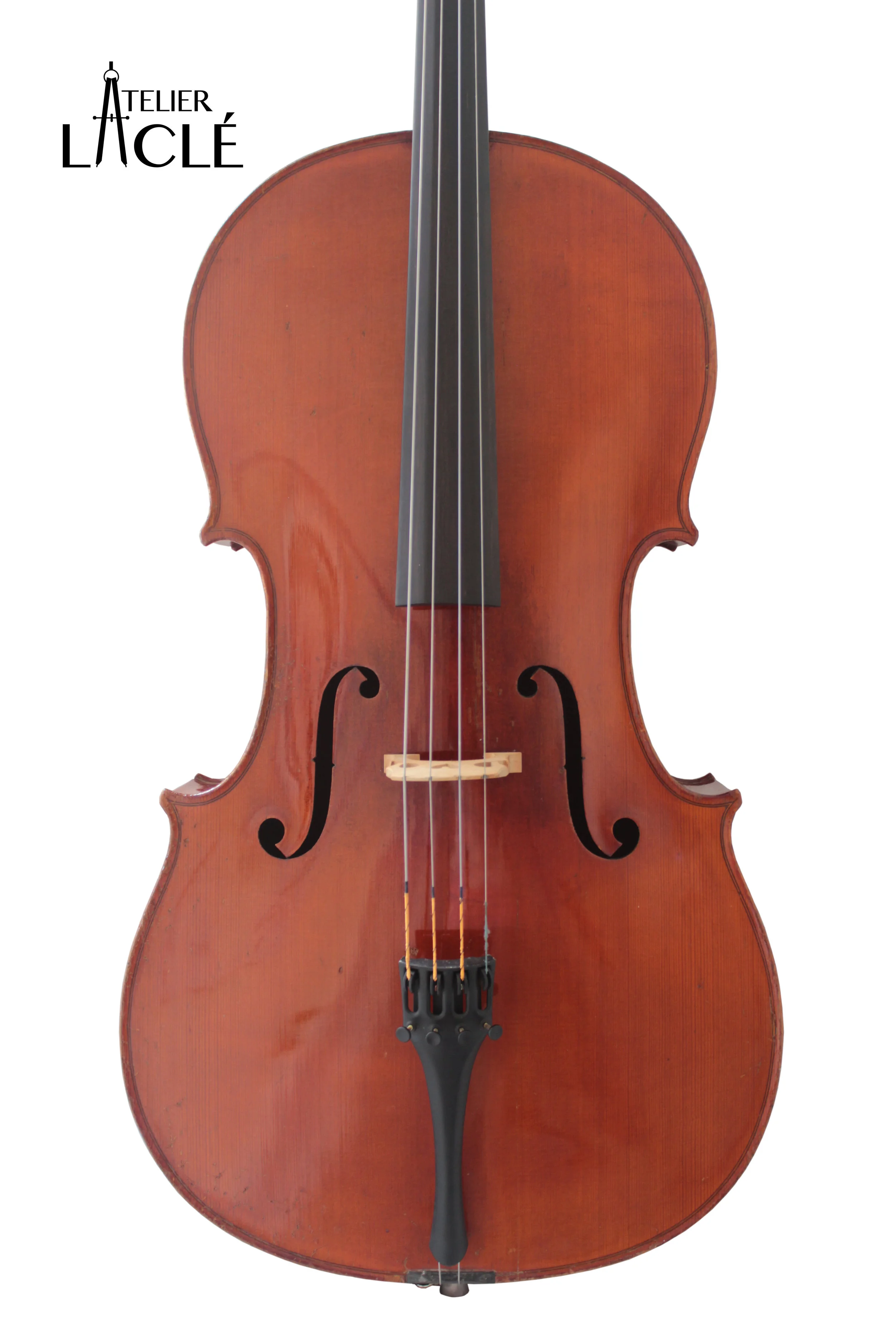


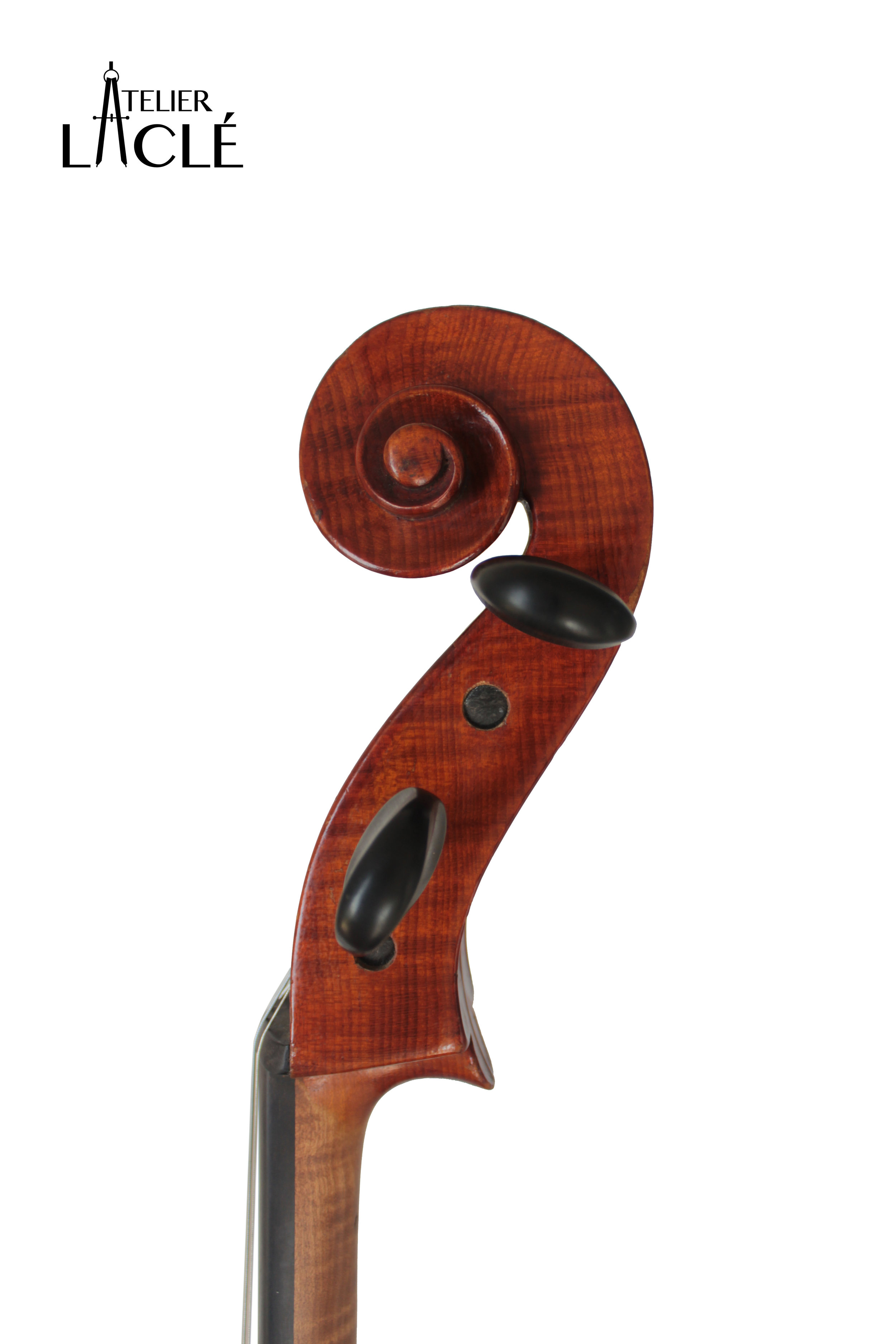